The Tan Delta Test, also known as the Loss Angle Test or Dissipation Factor Test, is a crucial diagnostic technique used in the field of electrical insulation testing. This test plays a vital role in assessing the health and condition of insulating materials, such as those found in cables, transformers, windings, and bushings. By measuring the dissipation factor or tan delta (tanδ) of the insulation, the test provides valuable insights into the quality, integrity, and aging of the insulation system.
In this article, we delve into the principles, methods, and significance of the Tan Delta Test. We explore how the behavior of insulators as capacitors, the presence of impurities, and the resistive component of leakage current impact the tan delta values. Furthermore, we discuss the importance of applying very low-frequency test voltages and the reasons behind it.
Additionally, we examine the process of predicting test results and the two approaches used for assessing insulation conditions. We also touch upon the different modes of the Tan Delta Test, including manual and automated methods. By understanding these aspects, we gain valuable knowledge about this essential testing technique used in the electrical industry.
Join us as we explore the Tan Delta Test in depth, unraveling its principles, methodologies, and applications. By the end of this article, you will have a comprehensive understanding of this crucial test and its role in ensuring the integrity and reliability of electrical insulation systems.
Principle of Tan Delta Test
The tan delta test, also known as the power factor test, is a widely used diagnostic technique to evaluate the insulation condition of electrical equipment. This test helps identify potential insulation problems and assess the overall health of the system. The principle behind the tan delta test lies in the measurement of dielectric losses in the insulation material.
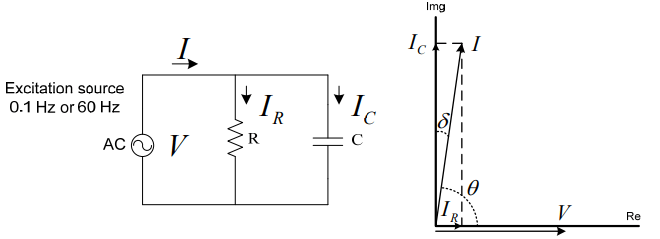
When an alternating current (AC) voltage is applied to the insulation, the insulation material exhibits certain losses due to various factors such as imperfections, contaminants, and aging.
These losses can be attributed to two components:
1. resistive losses (active power)
2. reactive losses (reactive power).
The resistive losses occur due to the presence of resistance in the insulation material. This resistance leads to the dissipation of energy in the form of heat.
On the other hand, the reactive losses occur due to the presence of capacitance and inductance in the insulation. These losses are associated with the storage and release of energy in the electrical field.
The tan delta is defined as the ratio of the reactive power to the active power in the insulation system. It represents the phase difference between the voltage and the current in the insulation material. Mathematically, it is the tangent of the angle between the voltage and current waveforms.
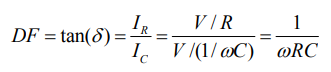
By measuring the tan delta, it is possible to assess the quality of the insulation and detect any deviations from its ideal behavior. A low tan delta value indicates a well-insulated system with minimal losses, while a high tan delta value suggests potential issues such as moisture ingress, degradation, or aging of the insulation.
The tan delta test is typically conducted at very low frequencies (VLF), usually in the range of 0.1 Hz to 0.01 Hz. Testing at these frequencies allows for better sensitivity and accuracy in detecting insulation problems. The test equipment applies a sinusoidal voltage to the insulation and measures the current response. By comparing the phase relationship between the voltage and current, the tan delta value is calculated.
Method of Tan Delta Testing
The Tan Delta Test is conducted using specialized equipment and follows a specific procedure to accurately measure the tan delta or loss angle of electrical insulation.
The test involves the application of a low-frequency test voltage to the insulation system and the measurement of the resulting leakage current. Here is an overview of the method involved in performing the Tan Delta Test:
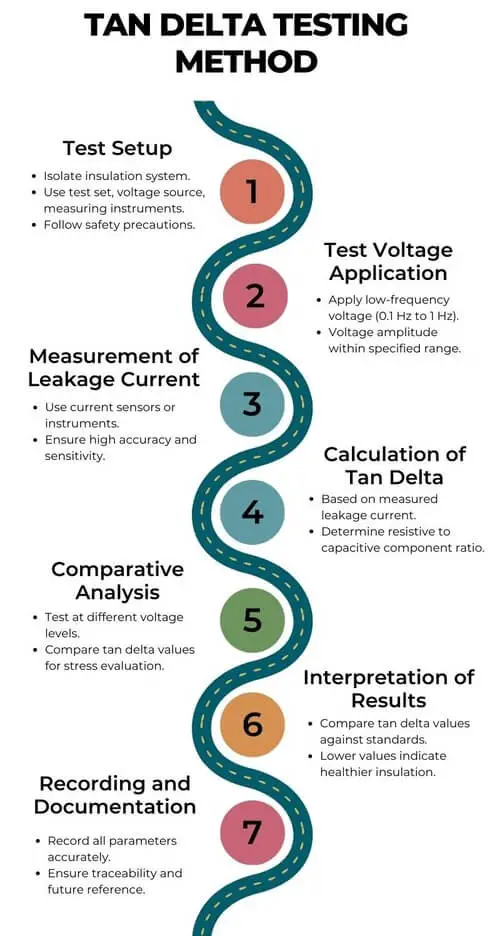
- Test Setup: To conduct the Tan Delta Test, the insulation system under examination must be isolated from the rest of the electrical network. The equipment required for the test includes a test set, voltage source, measuring instruments, and suitable connections. Proper safety precautions must be followed to ensure the safety of the personnel and equipment involved.
- Test Voltage Application: A low-frequency test voltage, typically in the range of 0.1 Hz to 1 Hz, is applied to the insulation system. The voltage amplitude should be within the specified range for the particular application. The applied voltage stimulates the insulation system and induces the leakage current.
- Measurement of Leakage Current: The leakage current resulting from the applied voltage is measured using appropriate current sensors and instruments. The measurements are typically performed using a current transformer or a Rogowski coil. The instruments used for measurement should have high accuracy and sensitivity to capture even small leakage currents.
- Calculation of Tan Delta: Based on the measured leakage current, the tan delta or loss angle is calculated. This involves determining the ratio of the resistive component to the capacitive component of the leakage current. The ratio can be obtained using mathematical calculations or through specialized instruments capable of directly providing the tan delta value.
- Comparative Analysis: In addition to measuring the tan delta at a specific voltage, it is common to conduct the test at different voltage levels. By comparing the tan delta values obtained at different voltages, it is possible to evaluate the insulation system’s behavior under varying stress conditions. This comparative analysis helps identify any significant changes or trends in the tan delta values, indicating potential insulation degradation or faults.
- Interpretation of Results: The tan delta values obtained during the test are compared against established standards or manufacturer specifications to determine the insulation’s condition. Lower tan delta values indicate healthier insulation with minimal leakage current and lower losses. Higher tan delta values may indicate the presence of moisture, contamination, aging, or other insulation issues that require further investigation or corrective measures.
- Recording and Documentation: All test parameters, including applied voltage, measured leakage current, and calculated tan delta values, should be recorded accurately. Proper documentation ensures traceability and provides a reference for future assessments or comparison with previous test results.
The method of Tan Delta Testing provides valuable insights into the condition of electrical insulation. It helps identify insulation degradation, enabling proactive maintenance and ensuring the reliability and safety of electrical systems.
Importance of Very Low Frequency:
In the field of electrical testing and diagnostics, Very Low Frequency (VLF) testing has gained significant importance, particularly in assessing the integrity and reliability of electrical insulation systems. VLF refers to the frequency range typically between 0.1 Hz and 0.01 Hz, which lies below the conventional power frequency range of 50 Hz or 60 Hz. Here are some key reasons why VLF testing holds such importance:
- Sensitivity to Insulation Defects: VLF testing is highly sensitive to insulation defects, such as voids, weak spots, and moisture, which are common causes of insulation breakdown. By subjecting the insulation system to a VLF test voltage, any existing defects are more likely to be identified. The low-frequency nature of VLF testing enhances the detection capability, enabling the early detection of insulation weaknesses before they escalate into more severe issues.
- Enhanced Dielectric Stress: VLF testing allows for the application of a higher effective voltage stress to the insulation system compared to traditional power frequency testing. This increased stress level helps accelerate the aging process and potential breakdown of the insulation, revealing any hidden weaknesses or aging-related issues. By applying an elevated stress level within a shorter testing duration, VLF testing can effectively simulate the long-term effects that insulation would experience during its operational life.
- Detection of Moisture and Contamination: Moisture ingress and the presence of contaminants are major concerns for electrical insulation systems. VLF testing is particularly effective in identifying such issues due to the increased sensitivity of insulation to these factors at low frequencies. Moisture and contaminants cause changes in the electrical properties of the insulation, resulting in an increase in the tan delta or loss angle values. By conducting VLF tests, these changes can be accurately measured, indicating the presence and severity of moisture or contamination within the insulation.
- Time-Efficient Testing: Compared to power frequency testing, VLF testing offers the advantage of shorter test durations while maintaining the same level of effectiveness. The ability to perform comprehensive insulation assessments within a shorter timeframe allows for efficient testing in various applications, such as routine maintenance, commissioning of new installations, and troubleshooting activities. This time efficiency not only reduces operational costs but also minimizes system downtime, ensuring uninterrupted power supply and operational continuity.
- Compliance with International Standards: VLF testing has gained wide acceptance and is often recommended by international standards organizations, such as the International Electrotechnical Commission (IEC) and the Institute of Electrical and Electronics Engineers (IEEE). Many industry-specific standards and guidelines advocate the use of VLF testing for evaluating the insulation condition of power cables, transformers, rotating machines, and other high-voltage equipment. Adhering to these standards ensures a standardized approach to insulation testing and facilitates accurate comparison and analysis of test results.
Thus Very Low Frequency (VLF) testing has become an integral part of electrical insulation diagnostics due to its sensitivity, ability to detect insulation defects and moisture, enhanced dielectric stress, time efficiency, and compliance with international standards. By utilizing VLF testing, maintenance personnel and engineers can assess the condition of electrical insulation systems with higher accuracy, make informed decisions regarding maintenance and repairs, and ensure the overall reliability and performance of electrical power systems.
Predicting Results of Tan Delta Testing
Tan Delta testing, also known as the Loss Angle or Dissipation Factor test, provides valuable insights into the condition and quality of electrical insulation systems. By measuring the power loss and phase angle between the applied voltage and the resulting current, tan delta testing enables the prediction of various outcomes related to the insulation. Here are some key factors and results that can be predicted through tan delta testing:
- Insulation Degradation: As electrical insulation ages or undergoes degradation, its dielectric properties can deteriorate, leading to increased power loss and changes in the phase angle. Tan delta testing can detect these changes and indicate the level of insulation degradation.
By monitoring the trend of tan delta values over time, it is possible to assess the rate of degradation and predict the remaining useful life of the insulation. This information allows for proactive maintenance planning and helps prevent unexpected failures. - Moisture Content: Moisture is one of the most common causes of insulation deterioration. Tan delta testing is highly sensitive to the presence of moisture within the insulation material. As moisture increases, the tan delta value typically rises, indicating a higher power loss and a change in the phase angle.
By analyzing the tan delta results, it is possible to predict the moisture content and assess the severity of moisture-related issues within the insulation system. This prediction enables targeted actions, such as drying or replacing moisture-affected components, to mitigate potential risks. - Contamination: Contaminants, such as dust, dirt, or conducting particles, can adversely affect the performance of electrical insulation. Tan delta testing helps identify the presence and severity of contamination within the insulation system. The introduction of contaminants increases the power loss and alters the phase angle, resulting in higher tan delta values.
By analyzing the tan delta results, maintenance personnel can predict the extent of contamination and take appropriate measures, such as cleaning or replacing contaminated components, to restore the insulation’s performance. - Detection of Partial Discharges: Partial Discharge (PD) activity within electrical insulation is a significant concern as it indicates the presence of localized defects or breakdowns. Tan delta testing can indirectly predict the occurrence of PDs by identifying anomalies in the insulation system.
As PDs cause changes in the electrical properties of the insulation, they result in altered tan delta values. By monitoring and analyzing the tan delta results, it is possible to detect potential PD issues and take preventive measures to avoid catastrophic failures. - Insulation Health Assessment: Tan delta testing provides a comprehensive assessment of insulation health by considering multiple factors, such as power loss, phase angle, moisture content, and contamination.
By analyzing these parameters, maintenance personnel can predict the overall condition of the insulation system, including any potential risks or issues. This predictive capability allows for informed decision-making regarding maintenance, repairs, or replacement, optimizing the reliability and performance of electrical equipment.
It is important to note that the prediction of results through tan delta testing requires a baseline comparison and an understanding of the specific equipment and insulation materials being tested. Establishing a reference baseline and tracking any deviations over time enable more accurate predictions and facilitate effective maintenance strategies.
In summary, tan delta testing allows for the prediction of insulation degradation, moisture content, contamination levels, detection of partial discharges, and overall insulation health assessment. By leveraging these predictive capabilities, maintenance personnel can proactively address insulation-related issues, minimize downtime, and ensure the long-term reliability and safety of electrical systems.
Tan Delta Test Modes
The tan delta test, also known as the power factor test, offers different modes of operation to suit various testing requirements and conditions. These modes provide flexibility and enable a comprehensive evaluation of the insulation system. Let’s explore the different modes of the tan delta test:
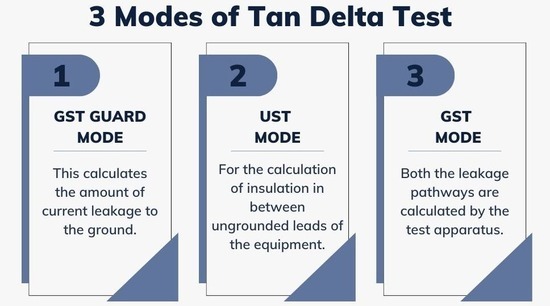
- GST Guard Mode: In this mode, the tan delta test calculates the amount of current leakage to the ground. The GST Guard mode eliminates the current leakage through the red or blue leads. The grounded edges are not included in the calculation.
When the GST Guard mode is applied to the device, the current measurement is only through the blue or red leads. The current flow through the ground lead is automatically bypassed to the AC source and excluded from the calculation. This mode helps determine the insulation condition by considering the leakage pathways to the ground. - UST Mode: The UST (Ungrounded Specimen Test) mode is employed to calculate the insulation between ungrounded leads of the equipment under test. In this mode, the individual portions of the insulation are separated and analyzed without any other insulation connected to them.
By isolating specific sections of the insulation, the UST mode allows for a focused assessment of their performance. It helps identify and evaluate the insulation characteristics between ungrounded components. - GST Mode: The GST (Grounded Specimen Test) mode is the final mode of operation in tan delta testing. In this mode, both leakage pathways are calculated by the test apparatus. The current, capacitance values, UST, and GST guards, as well as the loss in watts, need to be equal to the GST test parameters.
By comparing these values, the GST mode provides a comprehensive understanding of the insulation behavior. It considers both grounded and ungrounded components, giving a holistic view of the overall insulation performance.
It’s important to note that when the sum of the GST Guard and UST values is not equal to the GST parameters, it indicates potential issues with the test set or incorrect design of the test terminals. In such cases, further investigation or troubleshooting may be required to ensure accurate and reliable tan delta test results.
These different modes of the tan delta test allow for customized and detailed analysis of the insulation system, enabling effective condition assessment and maintenance of electrical equipment.
Conclusion
The tan delta test, also known as the power factor test, is a crucial diagnostic tool for assessing the insulation condition of electrical equipment. By measuring the tan delta, loss angle, and dissipation factor, this test helps identify potential issues and predict the performance and reliability of the insulation system.
In this article, we discussed the principle of the tan delta test, which is based on the measurement of the dielectric losses in the insulation material. We explored the method of conducting a tan delta test, including the necessary equipment and procedures involved. Additionally, we highlighted the importance of very low frequency (VLF) testing for more accurate and reliable results.
The tan delta test provides valuable information about the insulation condition, such as moisture content, aging, and degradation. By analyzing the results, electrical engineers and maintenance professionals can make informed decisions regarding equipment maintenance, repair, or replacement. Early detection of insulation problems through the tan delta test can prevent unexpected failures, reduce downtime, and improve overall system performance.
We also discussed the different modes of the tan delta test, including GST Guard mode, UST mode, and GST mode. Each mode offers specific insights into the insulation behavior, allowing for a comprehensive assessment of grounded and ungrounded components.
In conclusion, the tan delta test is an indispensable tool for evaluating insulation performance and ensuring the reliability of electrical systems. Regular tan delta testing can significantly contribute to the prevention of equipment failures, enhance safety, and prolong the lifespan of critical assets. By understanding the principles, methods, and importance of tan delta testing, professionals in the field of electrical engineering can effectively manage and maintain the insulation systems of various equipment.
Comments are closed.