An underground cable essentially consists of one or more conductors covered with suitable insulation and surrounded by a protecting cover.
Although several types of underground cables are available, the type of cable to be used will depend upon the working voltage and service requirements.
In general, an underground cable must fulfill the following necessary requirements :
- The conductor used in cables should be tinned stranded copper or aluminium of high conductivity. Stranding is done so that the conductor may become flexible and carry more current.
- The conductor size should be such that the cable carries the desired load current without overheating and causes voltage drop within permissible limits.
- The cable must have a proper thickness of insulation in order to give a high degree of safety and reliability at the voltage for which it is designed.
- The cable must be provided with suitable mechanical protection so that it may withstand the rough use in laying it.
- The materials used in the manufacture of cables should be such that there is completely chemical and physical stability throughout.
Construction of Cables
The figure shows the general construction of a three-conductor cable. The various parts are:
- Cores or Conductors
- Insulation
- Metallic sheath
- Bedding
- Armoring
- Serving
Parts of an Underground Cable
|
Cores or Conductors
A cable may have one or more than one core (conductor) depending upon the type of service for which it is intended. For instance, the 3-conductor cable shown in the figure is used for 3-phase service.
The conductors are made of tinned copper or aluminium and are usually stranded in order to provide flexibility to the cable. The larger the conductor, the greater the amount of current can flow through the conductor.
The aluminium or copper conductor carries the electrical current. Aluminium conductors are usually used for medium voltage distribution networks requiring long distances and extensive cabling. Copper cables are used for short links in substations and industrial installations where smaller cables or higher power transmitting properties are required.
The conductor behavior is characterized by two particularly noteworthy phenomena:
The skin effect is the concentration of electric current flow around the periphery of the conductors. It increases in proportion to the cross-section of the conductor used.
The short distance separating the phases in the same circuit generates the proximity effect.
In practice, the proximity effect is weaker than the skin effect and rapidly diminishes when the cables are moved away from each other.
The proximity effect is negligible when the distance between two cables in the same circuit or in two adjacent circuits is at least 8 times the outside diameter of the cable conductor.
Read: Bundled Conductors in Transmission Lines
Insulation
Around the conductor, it is necessary to provide insulation to prevent electrical short circuits.
Each core or conductor is provided with a suitable thickness of insulation, the thickness of layer depending upon the voltage to be withstood by the cable.
The insulation must be of sufficient thickness to withstand the electric field under the rated and transient operating
conditions. See the table on insulation thickness .
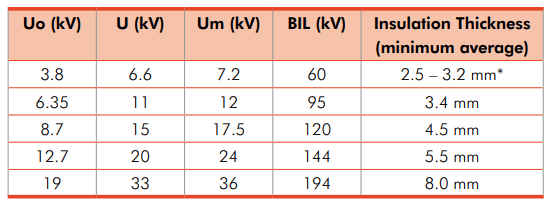
The commonly used materials for insulation are impregnated paper, varnished cambric, rubber, mineral compound.
In medium-voltage underground cables there are two main types of insulation material:
- XLPE (Cross-linked Polyethylene)
- The most common material for MV cables today.
- EPR – Ethylene Propene Rubber
- More flexible than XLPE but not as efficient at reducing losses in circuits as XLPE. Cables used in marine and offshore applications are normally constructed with EPR insulation.
Read more on different types of insulation materials used in underground cables.
Metallic sheath
In order to protect the cable from moisture, gases or other damaging liquids (acids or alkalies) in the soil and atmosphere, a metallic sheath of lead or aluminium is provided over the insulation as shown in Figure.
The main function of the metallic screen is to nullify the electric field outside of the cable – it acts as a second electrode of the capacitor formed by the cable. The screen needs to connect to earth at least at one point along the route.
The second function of the metallic screen is to form a radial barrier to prevent humidity from penetrating the cable insulation system.
When humidity and a strong electric field are present together, the insulation deteriorates by what is called water-treeing, which can eventually cause the insulation to fail.
Bedding
Over the metallic sheath is applied a layer of bedding which consists of fibrous material like jute or hessian tape.
The purpose of bedding is to protect the metallic sheath against corrosion and from mechanical injury due to armoring.
Armoring
Over the bedding, armoring is provided which consist of one or two layers of galvanized steel wire or steel tape.
Its purpose is to protect the cable from mechanical injuries while laying it or handling it. Armoring may not be done in the case of some cables.
Serving
In order to protect armoring from atmospheric conditions, a layer of fibrous material like jute similar to bedding is provided over the armoring. This is known as serving.
Armoring and serving are only applied to the cables for the protection of conductor insulation and to protect metallic sheath from mechanical injury.
Construction Details of Single Core XLPE Insulated Armoured PVC Sheath Underground Cable
The figure shows a circular compacted stranded copper or aluminium conductor, XLPE insulated, with copper tape screened and covered with extruded PVC bedding, aluminium wire armored and PVC outer sheath.
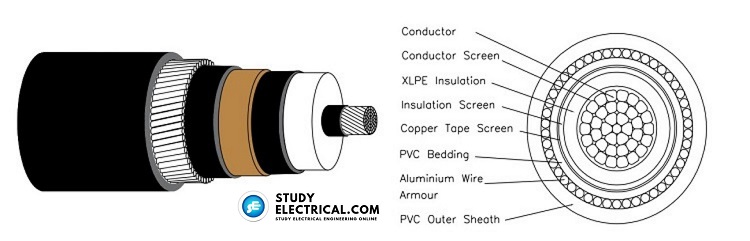
Conductor
Plain circular compacted stranded copper or aluminium conductor to IEC 60228 class 2.
Conductor Screen
An extruded layer of semiconductive compound.
Insulation
XLPE (cross-linked polyethylene) rated at 90 degrees C.
Insulation Screen
- Non-metallic part
An extruded layer of semiconductive compound. - Metallic part
Copper tape screen (SCT).
Bedding
The extruded layer of PVC ST2 compound.
Armour
Aluminium wires shall be applied helically over the PVC bedding.
Outer Sheath
PVC type ST2 to IEC 60502 color black.
Reference: powerandcables.com
Comments are closed.