Thin-film technology has become a crucial element in today’s modern world. It’s in the mobile phone that wakes you up every morning, the computer screen you work with during the day, and the mirror you face when brushing your teeth at night.
And while thin film is, perhaps, one of the most overlooked elements of technology, it’s been around since ancient civilizations. Over 5,000 years ago, the Egyptians embellished their statues and artifacts with gold coatings using similar techniques to thin-film applications.
This article discusses the different thin-film applications in electronics and modern equipment.
What Is Thin Film?
In its most basic sense, thin films change the surface interactions of the platforms it’s added. For example, they’re used to create an edge on cutting tools, giving them the hardness and low-friction properties required. Automobile parts that need protection from ultraviolet rays use chromium films to develop hard, metallic coatings, resulting in cost and weight savings.
In oversimplified terms, thin films are layers of materials deposited on a substrate to give it the physical and chemical properties it needs. When they say “thin,” this can range from a single atom to several nanometers. If you want a deep dive into the intricate process, Korvus Technology wrote a comprehensive guide on the thin film deposition process.
Thin Film Applications
As alluded to above, different deposition processes are used for varying thin-film applications. The applications listed below are categorized based on these processes.
Zinc Oxide-Based Thin Film
Zinc Oxide (ZnO) is a popular thin film for several reasons. These include the following:
- Readily available
- Inexpensive
- Excellent conductivity
- Physically and chemically stable
Meanwhile, ZnO thin-film applications include the following:
- Solar cells
- Semiconductor devices and coatings
- Displays (such as LED and OLED)
- Sensors (such as biosensors and gas sensors)
- Lasers
ZnO’s versatility and cost-effectiveness have made it an attractive material for various applications across different industries.
Thin Film For Solar Cells
While ZnO thin film has solar cell applications, copper indium gallium has become a viable alternative in the solar energy sector due to its higher efficiency and enhanced stability. In general, thin-film solar cells provide clean and low-cost energy generation, making them a critical component of the alternative energy industry.
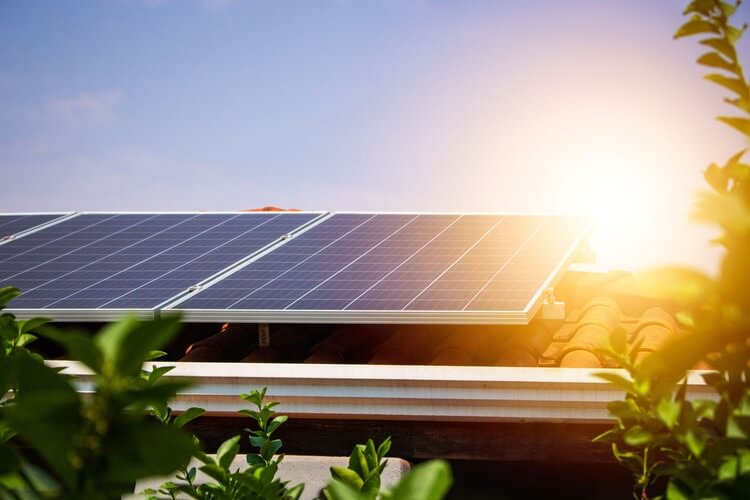
Additionally, thin-film solar cells possess an absorber layer with a high absorption coefficient, which allows for a reduction in cost and material thickness.
Thin-Film Battery
While lithium-ion batteries power most of the devices, equipment, and vehicles used today, thin-film batteries have emerged as a better alternative. They’re thinner and lighter, making them ideal for tech devices that are getting slimmer and slimmer. In fact, thin-film batteries are now used in the medical industry to power implant devices.
And while they’re also lighter and denser, they don’t sacrifice current and voltage capacity.
Thin-Film Resistors
Thin-film resistors are another popular application in modern technology. Their applications include the following:
- Radio receivers
- Circuit boards
- Radiofrequency devices
- Wireless routers
- Bluetooth modules
- Monitors
More specifically, nickel-chromium alloy-based resistors enjoy widespread use in smaller and thinner electronic devices. Owing to their high resistivity, these thin-film resistors improve electrical performance and reliability when embedded into a printed wiring board. And when alloy is combined with small amounts of aluminum and silicon, they can lead to better temperature stability.
Optical Thin Films
Optical coatings and various optoelectronics use optical thin films. The coatings in these thin films, such as those in lenses used in glasses, telescopes, and mirrors, affect how optics reflect and convey light. These coatings can be anti-reflective or highly reflective, which could deflect or filter light.
Thin-Film Coating
Manufacturers can use different techniques to achieve specific chemical and mechanical properties that can result in applications such as:
- Anti-reflective coating
- Ultraviolet/infrared coating
- Anti-scratch coating
- Lens polarization
- Anti-corrosion coating
- Hard coating
As you can imagine, these coatings can have many practical applications across various industries and technologies.
Final Words
There are three primary types of thin films. These include the following:
- Transparent Conductive Oxide (TCO) coatings: These are transparent electrical conductors used in technologies such as touchscreens, photovoltaics, and solar-cell thin films.
- Diamond-Like Carbon (DLC) coatings: These thin films increase a material’s hardness and scratch resistance, which are used to improve the durability of technologies like microelectronics and sensors.
- Anti-Reflective/High-Reflectivity (AR/HR) coatings: As discussed earlier, these coatings alter the optical properties of a material by filtering or reflecting light.
As thin-film deposition techniques and technology evolve, their applications will only grow. And while it will never be as celebrated as the products they’re integral to, thin films will continue to be a critical component of the modern world.