Programmable Logic Controllers (PLCs) are also referred to as programmable controllers in some places. They are widely used in commercial and industrial applications.
Basically, a PLC monitors inputs, makes decisions based on its program, and controls outputs to automate a process or machine. This article will give you basic information on the basic functions and configurations of PLCs.
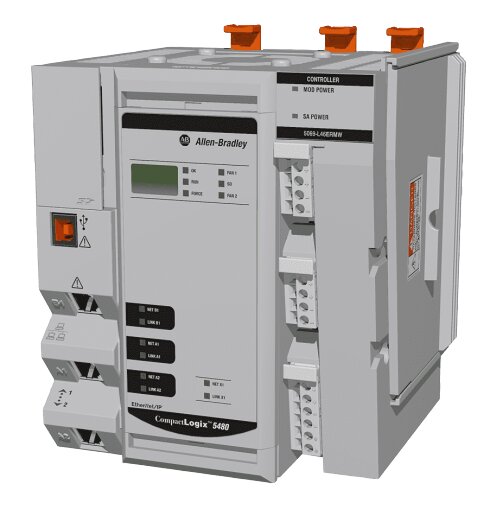
Basic PLC Working
A programmable logic controller (PLC) consist of the following parts
- Input modules or points
- Central Processing Unit (CPU)
- Output modules or points.
- Programming device
- Operator Interface device
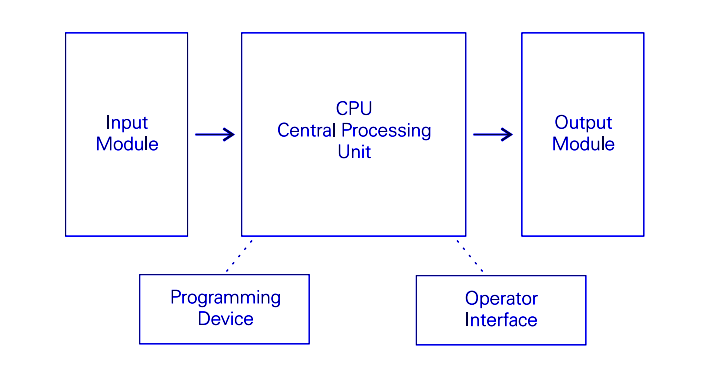
An input module accepts a variety of digital or analog signals from various field devices (sensors) and converts them into a logic signal. This logic signal can be used by the CPU.
The CPU makes decisions and executes control instructions. It is completely based on program instructions in memory.
Output modules are used to convert control instructions from the CPU into a digital or analog signal. This signal can be used to control various field devices (actuators).
A programming device is used to input the desired instructions to the PLC. These instructions given to the PLC determine what the PLC will do for a specific input.
An operator interface device is also used. This allows process information to be displayed and new control parameters to be entered.
Example of PLC Application
In this example a PLC is used to start and stop a motor. Pushbuttons are used as sensors are connected to the PLC inputs. A motor starter is connected to the output of the PLC.
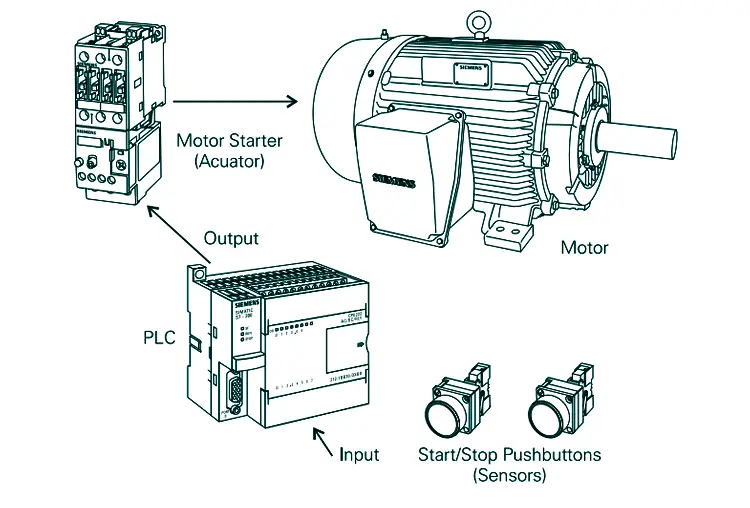
The pushbuttons can be used to start and stop a motor connected to a PLC through a motor starter (actuator).
Hard-Wired Control
Before the invention of PLCs, many of these control tasks were solved with contactor or relay controls. This is often referred to as hardwired control.
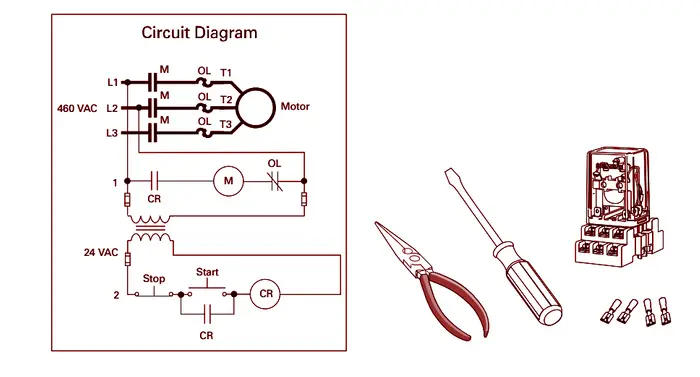
In hard wired control circuit diagrams had to be designed, electrical components specified and installed, and wiring lists created. Electricians wire the components necessary to perform a specific task.
If an error was made the wires had to be reconnected correctly. A change in function or system expansion required extensive component changes and rewiring.
Advantages of PLCs
The same, as well as more complex tasks, can be done with a PLC. Wiring between devices and relay contacts is done in the PLC program. Hard-wiring, though still required to connect field devices, is less intensive.
Modifying the application and correcting errors are easier to handle. It is easier to create and change a program in a PLC than it is to wire and rewire a circuit.
Following are just a few of the advantages of PLCs:
- Smaller physical size than hard-wire solutions.
- Easier and faster to make changes.
- PLCs have integrated diagnostics and override functions.
- Diagnostics are centrally available.
- Applications can be immediately documented.
- Applications can be duplicated faster and less expensively