When there is high dependence on test and measurement equipment in an industry, it is imperative to ensure that the equipment is accurate and reliable. Every instrument needs maintenance to compensate for wear and tear. Over time, even the best instruments will lose precision. Therefore, the need for calibration.
What is Calibration?
When an instrument fails to produce results as mentioned in the specifications, it needs to be adjusted through standardized techniques to ensure continuity in producing accurate results. This process of adjusting the equipment to conform with specifications is known as calibration. It is a form of preventive maintenance for test and measurement (T&E) equipment and helps avoid equipment malfunction.
The process may be carried out at designated calibration centers or even labs or sites where they are being used. Based on the instrument and precision required, the calibration process may last from a few minutes to a few days.
A thorough inspection checklist can be invaluable for guiding your calibration process. To help you with this crucial step, you can read more helpful articles from reputable websites.
Which Instruments Need Calibration?
All T&E instruments, from calipers and scales to balances and clamp meters, need regular calibration. Instruments like torque wrenches, clamp meters, barometers, micrometers, insulation units, incubators and centrifuges also need it.
Industries like research, medicine, food, mining and manufacturing rely on measurements to form conclusions and need to ensure that their test and measurement instruments are calibrated regularly to produce results in-line with their specifications.
Failing to calibrate the equipment has many downsides.
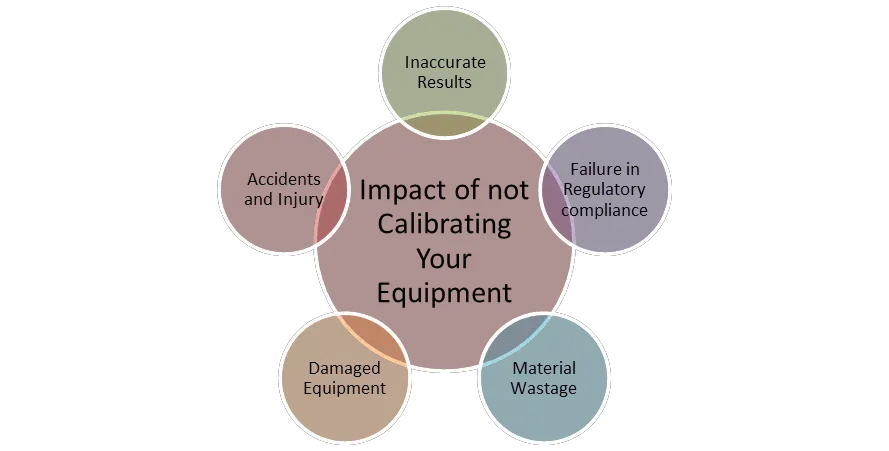
Data Source: https://www.usalab.com/blog/what-happens-when-you-dont-calibrate-your-lab-equipment/
Statistics reveal that 97% of R&D engineers agree that preventive maintenance can help avoid huge revenue losses. In fact, 53% of reported losses that exceed $100,000 per day are due to downtime caused by equipment malfunction.
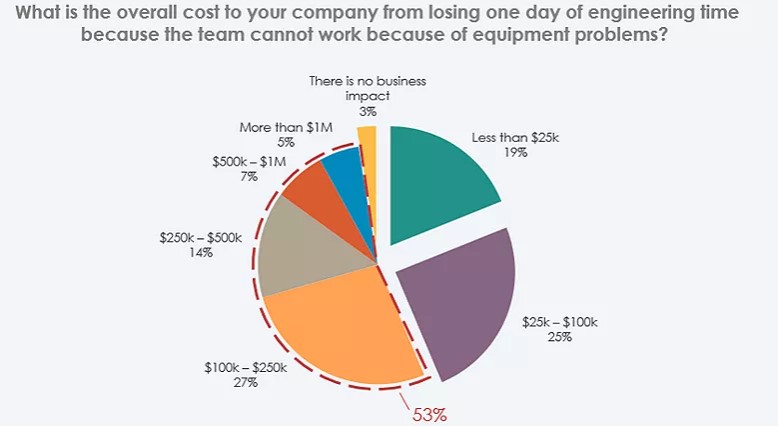
It comes as no surprise, therefore, that the Global Laboratory Equipment Services Market is estimated to steadily grow at a CAGR of 14.2% to reach $26.8 billion by 2026.
5 Rules to Follow for Effective Calibration of T&M Equipment
1. Know when to calibrate
It is crucial to ensure that instruments are calibrated:
- After any major incident or accident
- At regular intervals, as mentioned in the specification documents
- Before any major or highly impactful test is conducted
- When equipment is used after a long time
- Whenever the results seem to deviate from expected or standard results even slightly.
Refer to your manufacturer’s recommendations, and keep an eye on your instrument’s performance. If you notice any drift or inconsistencies, it’s time for a calibration check-up.
2. Follow standardized procedures
The calibration industry follows ISO specified standards. In addition, every industry and business has its own specific tolerance limits. Ensure that the calibration is done through standardized practices and the use of top quality equipment. The most common standard globally followed today is ISO/IEC 17025. Additionally, there are certain local and industry-specific standards to be followed as well. Choose a service provider that conforms with the regulations and is accredited according to your industry requirements.
If your organization lacks standardized procedures, take the initiative to create them. Collaborate with your team, consult experts and reference industry standards. Once you have your procedures in place, make sure everyone knows where to find them and understands the importance of following them.
3. Ask for and maintain traceability records
If you are outsourcing calibration services, make sure to ask for traceability records. These records help in understanding how much deviation was there, if any, how it was corrected, and whether the instrument now adheres to acceptable tolerance margins. Most importantly, it helps in understanding whether the instrument falls in the category of equipment to be used, repaired or discarded post calibration tests.
You may also request a traceability certificate from the calibration provider. This certificate should detail the standards used, the measurement uncertainties, and the accreditation of the calibration laboratory. Keep these records on file, as they are essential for demonstrating compliance with quality standards and regulations.
4. Ensure the accuracy of calibrating equipment
A key aspect of calibration is the instruments used for calibration. They should conform with the industry standards and ensure high precision. Calibration equipment itself should be checked against ideal metrics. Make sure the calibration service offers verification and adjustment to OEM specification, using NIST traceable equipment.
Ensure that your equipment’s calibration is traceable to a recognized national or international standard. This means that the calibration was performed using standards that are themselves traceable to a higher authority, creating an unbroken chain of accuracy.
Also, remember that the environment in which you store and use your calibration equipment can significantly impact its accuracy. Temperature, humidity, and vibrations can all introduce errors. Store your equipment in a controlled environment and be mindful of environmental conditions during use.
Additionally learn about point adjustments to understand 3-point and 5-point calibration procedures and decide which one fits your needs. When outsourcing, ask for accreditation and calibration certificates to ensure best results.
5. Follow a before and after approach
This is a major responsibility for the instrument owners and users. Before sending out the equipment, perform some standardized tests and make notes. After the instruments are calibrated, verify the certificates and re-conduct all tests to check whether the traceability reports match the identified deviations that are now seen with the new results. This ensures credibility of results and measurements.
Calibration is no child’s play. Confirming to standards, having the appropriate tools and report generation capacity, and ensuring accurate results requires expertise and years of experience with industry-wide equipment. So, choose your calibration service provider carefully.