A three phase asynchronous motor, commonly known as an induction motor, is a type of electric motor that operates on the principles of electromagnetic induction. It is called “asynchronous” because the rotor does not rotate at the same speed as the magnetic field produced by the stator, a phenomenon known as “slip.” These motors are widely used in industrial and commercial applications due to their robustness, reliability, and efficiency.
Basic Components and Working Principle
- Stator: The stationary part of the motor, which produces the rotating magnetic field. It consists of a core made of laminated steel and windings that carry the three phase current.
- Rotor: The rotating part of the motor, which is placed inside the stator. The rotor can be of two types: squirrel cage or wound (slip ring).
- Other Parts: Bearings, shaft, cooling fan, and enclosure are additional components that ensure smooth operation and durability.
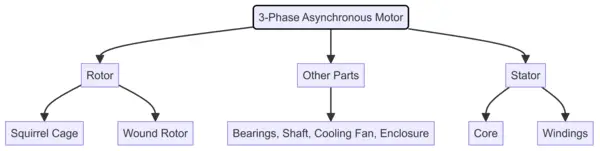
Working Principle
The operation of a three phase asynchronous motor is based on the principle of electromagnetic induction. When a three phase current flows through the stator windings, it creates a rotating magnetic field. This field induces a current in the rotor, producing a magnetic field that interacts with the stator’s field. The interaction of these magnetic fields generates a torque that causes the rotor to turn, thereby converting electrical energy into mechanical energy.
Types of Three-Phase Asynchronous Motors
Three-phase asynchronous motors come in two primary types: squirrel cage induction motors and slip ring induction motors.
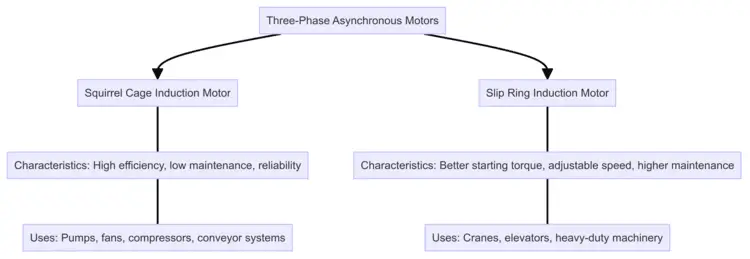
Squirrel Cage Induction Motor
The squirrel cage induction motor is the most common type, known for its simple and rugged construction. It features a rotor made of conductive bars short-circuited by end rings, resembling a squirrel cage. These motors are widely used in applications where a constant speed is required.
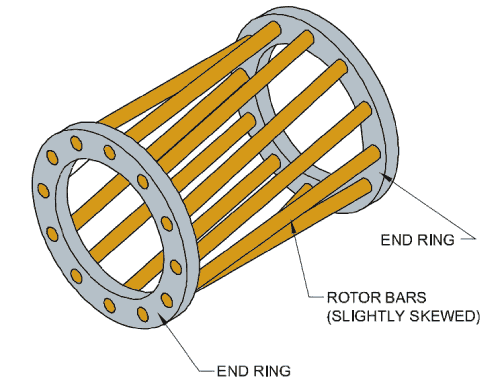
- Characteristics: High efficiency, low maintenance, and reliability.
- Uses: Pumps, fans, compressors, and conveyor systems.
Slip Ring Induction Motor
The slip ring induction motor, also known as a wound rotor motor, has a rotor with windings connected to slip rings. This design allows for external resistance to be added to the rotor circuit, providing better control over the motor’s starting and running characteristics.
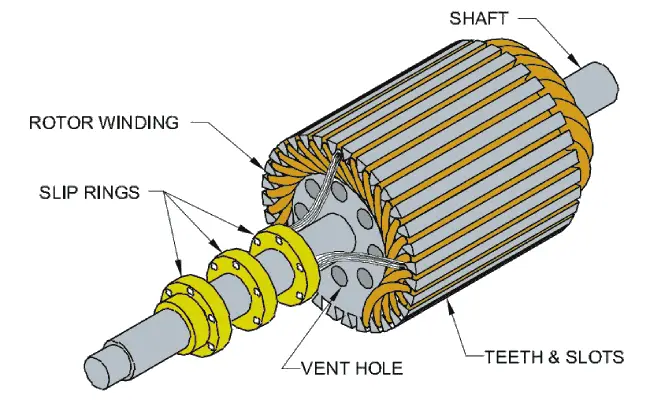
- Characteristics: Better starting torque, adjustable speed, and higher maintenance requirements.
- Uses: Cranes, elevators, and heavy-duty machinery requiring variable speed control.
Comparisons
- Efficiency: Squirrel cage motors are generally more efficient than slip ring motors.
- Maintenance: Squirrel cage motors require less maintenance due to their simpler construction.
- Starting Torque: Slip ring motors offer higher starting torque and better speed control.
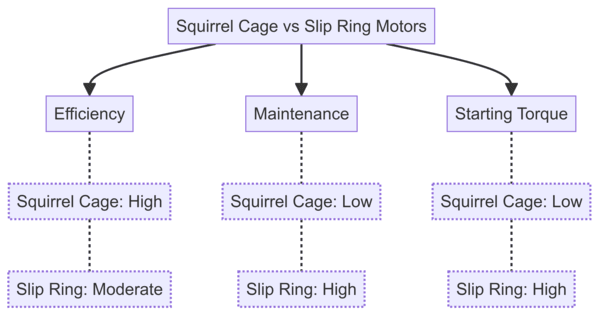
Construction and Design
The construction of a three phase asynchronous motor involves various components designed to optimize performance and durability.
Stator Construction
The stator is made up of a core constructed from laminated steel to reduce eddy current losses. It has slots where the three-phase windings are placed. These windings are typically made of copper or aluminum and are arranged to create a rotating magnetic field when energized.
Rotor Construction
The rotor can be either a squirrel cage or wound type. The squirrel cage rotor consists of conductive bars embedded in a laminated steel core, connected by end rings. The wound rotor, on the other hand, has windings similar to the stator, connected to slip rings that allow for external resistance to be added.
Windings and Magnetic Field
The windings in the stator are crucial for creating the rotating magnetic field. When a three-phase current flows through these windings, it produces a magnetic field that rotates around the stator. This rotating field induces a current in the rotor, causing it to turn and produce mechanical motion.
Operating Principles
Understanding the operating principles of three phase asynchronous motors is key to appreciating their functionality and performance.
Induction Process
The induction process is fundamental to the operation of these motors. When the stator’s rotating magnetic field cuts through the rotor, it induces an electromotive force (EMF) in the rotor conductors. This induced EMF generates a current in the rotor, which in turn produces its own magnetic field. The interaction between the stator and rotor magnetic fields generates torque, causing the rotor to rotate.
Slip and Synchronization
Slip is a crucial concept in asynchronous motors. It is defined as the difference between the synchronous speed (the speed of the rotating magnetic field) and the actual speed of the rotor. Slip is necessary for the induction process to occur, as it creates the relative motion needed to induce EMF in the rotor. The motor’s efficiency and performance are influenced by the slip, with optimal performance occurring at a certain slip percentage.
Torque Production
Torque production in a three phase asynchronous motor is a result of the interaction between the stator and rotor magnetic fields. The magnitude of the torque depends on the strength of these fields and the slip. The motor’s torque-speed characteristic curve shows how the torque varies with speed, highlighting different operating regions such as starting, peak torque, and stable operation.
Performance Characteristics
Three-phase asynchronous motors are valued for their performance characteristics, which include efficiency, speed-torque relationship, and power factor.
Efficiency
The efficiency of an asynchronous motor is influenced by various factors, including design, construction, and operating conditions. High-quality materials, precision engineering, and proper maintenance contribute to optimal efficiency. Losses in the motor, such as core losses, copper losses, and mechanical losses, should be minimized to enhance efficiency.
Speed-Torque Characteristics
The speed-torque characteristic curve of a three phase asynchronous motor illustrates the relationship between the motor’s speed and the torque it produces. This curve typically shows high torque at low speeds (starting torque), a peak torque at a certain slip, and a gradual decrease in torque as the speed approaches synchronous speed. Understanding this curve helps in selecting the right motor for specific applications.
Power Factor
The power factor of an asynchronous motor is a measure of how effectively it converts electrical power into mechanical power. A high power factor indicates efficient power usage, while a low power factor suggests inefficiencies. Various techniques, such as using power factor correction capacitors, can improve the motor’s power factor.
Starting Methods
Starting methods are crucial for ensuring smooth and efficient operation of three-phase asynchronous motors. Different methods are used based on the motor type and application requirements.
Direct On-Line (DOL) Starting
DOL starting is the simplest and most common method, where the motor is directly connected to the power supply. It offers a straightforward and cost-effective solution but can result in high inrush currents and mechanical stress on the motor.
- Advantages: Simple and inexpensive.
- Disadvantages: High inrush current, mechanical stress.
Star-Delta Starting
Star-delta starting reduces the inrush current by initially connecting the motor windings in a star configuration, then switching to a delta configuration for normal operation. This method is commonly used for motors with higher power ratings.
- Advantages: Reduced starting current, lower mechanical stress.
- Disadvantages: More complex circuitry, transition time between star and delta.
Auto-Transformer Starting
Auto-transformer starting uses an auto-transformer to reduce the voltage applied to the motor during startup, thereby limiting the inrush current. Once the motor reaches a certain speed, the full voltage is applied.
- Advantages: Controlled starting current, suitable for larger motors.
- Disadvantages: Higher cost, more complex setup.
Control and Maintenance
Proper control and maintenance are essential for the reliable and efficient operation of three-phase asynchronous motors.
Control Techniques
Control techniques for these motors include variable frequency drives (VFDs) and soft starters. VFDs allow precise control of motor speed and torque by varying the frequency and voltage of the power supply. Soft starters limit the inrush current during startup, reducing mechanical stress and improving motor lifespan.
Maintenance Practices
Regular maintenance practices include inspecting and cleaning motor components, checking electrical connections, lubricating bearings, and monitoring temperature and vibration levels. Preventive maintenance helps in identifying potential issues early and ensuring continuous operation.
Troubleshooting
Common problems with three phase asynchronous motors include overheating, excessive noise, and vibration. Troubleshooting involves diagnosing the root cause of these issues, such as electrical faults, misalignment, or bearing wear, and implementing corrective measures.
Applications of Three-Phase Asynchronous Motors
Three phase asynchronous motors are used in a wide range of applications due to their versatility and reliability.
Industrial Uses
In industrial settings, these motors power machinery such as pumps, compressors, conveyor systems, and fans. Their robustness and ability to handle varying loads make them ideal for heavy-duty applications.
Commercial Uses
Commercial applications include HVAC systems, elevators, and escalators, where consistent performance and efficiency are critical. These motors are also used in commercial building automation systems.
Special Applications
Special applications of three phase asynchronous motors include electric vehicles, renewable energy systems, and marine propulsion. Their adaptability and performance characteristics make them suitable for innovative and emerging technologies.
Advantages and Disadvantages
Understanding the advantages and disadvantages of three phase asynchronous motors helps in making informed decisions for their use.
Pros
- Efficiency: High efficiency in converting electrical power to mechanical power.
- Reliability: Robust construction and low maintenance requirements.
- Versatility: Suitable for a wide range of applications.
- Cost-Effective: Lower initial and operating costs compared to other motor types.
Cons
- Starting Torque: Lower starting torque compared to some other motor types.
- Power Factor: Potentially lower power factor, requiring correction techniques.
- Speed Control: Limited speed control capabilities without additional equipment.
Future Trends and Innovations
The future of three phase asynchronous motors is shaped by technological advancements and the demand for energy-efficient solutions.
Technological Advancements
Recent developments include the use of advanced materials, improved design techniques, and smart monitoring systems. These innovations enhance motor performance, reliability, and efficiency.
Energy Efficiency Improvements
Energy efficiency is a key focus, with new motor designs and technologies aimed at reducing energy consumption and minimizing losses. Regulations and standards are also driving the adoption of more efficient motors.
Integration with Modern Systems
Three phase asynchronous motors are increasingly integrated with modern control systems, such as IoT and AI-based monitoring solutions. These integrations enable predictive maintenance, remote monitoring, and enhanced performance optimization.
Conclusion
Three phase asynchronous motors are a cornerstone of industrial and commercial applications due to their efficiency, reliability, and versatility. Understanding their construction, operating principles, and performance characteristics is essential for maximizing their potential.
As technology continues to advance, these motors are poised to become even more efficient and adaptable, meeting the evolving needs of various industries. The future holds exciting possibilities for three-phase asynchronous motors, driven by innovations in materials, design, and control systems.
For businesses and engineers, staying informed about these developments will be crucial in harnessing the full capabilities of these remarkable machines.